Measurement is performed with a confusing amount of cables, connectors, adapters, tools and equipment,
not to mention the weird software.
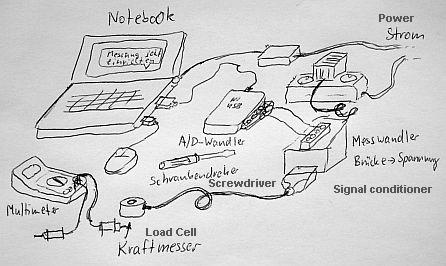
Suppose you want to measure a mechanical force with a strain-gauge load cell,
you need a couple of devices as shown in the picture.
For simplicity and cost-efficiency, I would use a
NI USB DAQ device „NI USB-6008“
containing the
ADS7870 chip.
Despite the low performance of 12 bit accuracy and 10 kSa/s overall sample rate,
this device is USB bus powered and therefore easy to use.
With a
self-made signal conditioner containing a DC/DC converter
to get power from „NI USB-6008“ device, no extra power supply is needed,
and the overall design is capable for in-field measurements.
However, some efford is needed to get this, and you have to calibrate all!
Too much to do for a routine job.
Moreover, a software must be built using LabVIEW
(that's easy) and calibrated
(that's a bit more complicated).
Tools
- Screwdriver to connect wires
- Multimeter to check voltages and connections, for troubleshooting
- A mass unit to check whether the force sensor works properly
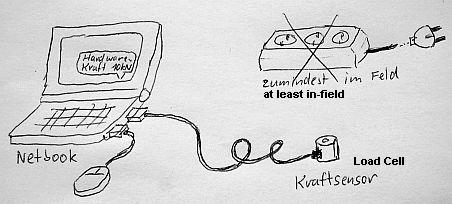
Every modern human outside who wants to measure a mechanical force
thinks that such constellation is easily available and ready to use.
Power is sorced from the (even more lightweight) netbook.
This is not available nowadays!
But it should be. And is expected by non-professionals.
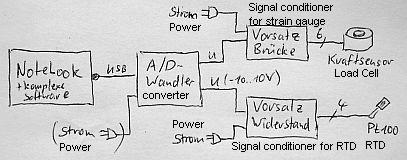
Suppose you want to measure
mechanical force (strain-gauge load cell) and
temperature (Pt100).
For a cartoon picture too confusing, I decided to draw a block diagram for the devices needed.
So suppose you have a „NI USB-6008“ for analog-digital conversion.
You need
two different signal conditioners,
for industrial application always with its own power supply and calibration issues.
Probably a better, faster A/D converter is necessary;
at least all the National Instruments devices need extra power too.
With a suitable and modular system like
HBM
Spider8,
MGCplus,
QuantumX
or
NI
cDAQ-9172,
it's easier to handle,
but still you have to solder some wires and plugs, and the overall cost is overwhelming.
Extra Power is also needed, and as all devices are made for mains supply, the power consumption is not suited for in-field battery powering.
No one of those systems are powerable by a notebook.
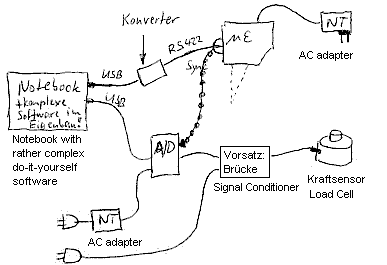
Things get worse when you already have a “smart” sensor with digital output, like
Micro-Epsilon µε optoNCDT2200.
This Laser Triangulation Sensor outputs distances (± 10 mm) with 15 bit resolution (< 1 µm)
at pretty fast 10 kSa/s.
A PC built-in serial interface with its maximum 115.2 kBaud is too slow.
So you need a special
adapter for connecting.
For USB as
Do-It-Yourself device
to keep costs in bounds.
The next problem is to prevent drifting of another A/D converter, i.e.
synchronization. You need an extra
Sync Wire. Really!
But this imposes
three assumptions:
- A sync output
- A piece of cable (you have to solder plugs yourself, there is no standard!)
- A sync input for the next A/D converter
- Good luck that voltages etc. are the same, e.g. TTL level,
otherwise, you have to create some convertion circuitry and its power supply
The second sensor (here a strain-gauge load cell) works as before,
with signal conditioner.
Moreover, some sort of a start trigger is needed (depending on latency and demands),
so you may need another sync cable, not shown in the picture.
If you have two “smart” sensors with no synchronization between,
you must do it later by resampling in software if necessary.
Note that resampling is not measuring but interpolating values where no values were.
Same applies for AC measurements (e.g. sound pressure, modal analysis) per sound card.